Managing the issue of combustible composite panels within your food and drink organisation
The risks of combustible composite panels are widely acknowledged, as older nonapproved panels have caused significant fires across the food & drink sector.
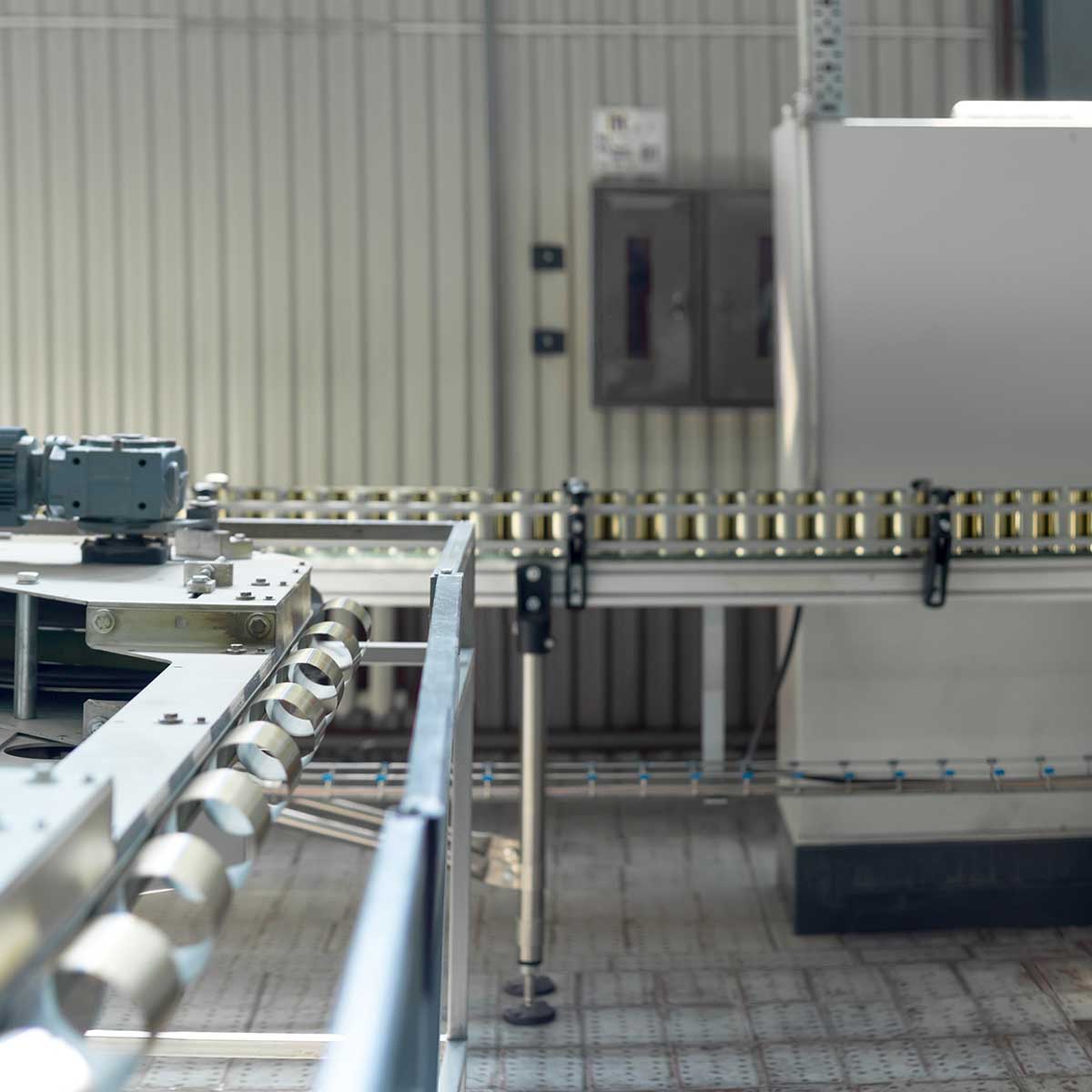
The risks of combustible composite panels are widely acknowledged, as older nonapproved panels have caused significant fires across the food & drink sector. While more modern (LPS1181/FM4880 approved) and non-combustible panels are acceptable to the insurance market, the reality is that many food premises still have combustible composite panels in place across significant areas.
The food & drink sector was particularly impacted by the hardening of the UK property insurance market towards combustible composite panels and a risk that was deemed acceptable prior to the change in the market is now much less attractive to insurers.
Whilst there is an understanding of the insurance market’s approach to food & drink organisations, the levels of premiums, the terms and conditions and capacity levels provided remain a concern for many organisations.
With a ‘new normal’ established in the market’s approach, what should food and drink organisations be looking to do in order to mitigate the risks and manage their combustible composite panels?
Preventative measures
Where any type of risk exists, there are four core areas to consider, known as the four ‘T’s, which can be applied to the issue of combustible composite panels, as follows:
Terminate
Stop higher risk processes or replace combustible panels. While the ‘cost versus benefit’ analogy works well for panel replacement and associated savings, it can cause operational issues. A number of food manufacturers have ceased their high risk activities, such as frying lines, in order to access better insurance solutions.
Tolerate
Accept the risk as it is. However, as the market may change again, this approach could carry a further risk and, in some cases, some organisations would find themselves with limited options other than their current insurance carrier.
Treat
If it’s not possible to terminate the risk and it’s not considered tolerable, you need to treat it. In the case of combustible composite panels, this involves looking at other measures to reduce the risk, such as:
- Install active fire suppression at building level (sprinklers) or process level (watermist systems for fryers; gaseous suppression systems for electrical control panels).
- Install passive fire protection at building level. (This presents some challenges within the food sector as there is a need for openings within the walls. While insurers won’t accept fire shutter protected openings as a full divide, it furthers their acceptance or consideration of the risk, encouraging them to provide a greater level of capacity.)
- Undertake partial panel replacement in higher risk areas (for example, processing areas are generally more hazardous than cold stores).
- Improve maintenance standards by continually monitoring the condition of key equipment, increasing the frequency of electrical inspections and utilising thermographic imaging. Key inception risks could also be moved away from the main risk building – for example, construct forklift truck charging facilities externally.
- Install comprehensive automatic fire detection with remote signalling. While this won’t reduce the outcome in the event of a significant fire, it will help small issues to be identified and addressed before leading to fire. (There are challenges and costs in automatic fire detection in food premises due to the potential for false alarms as a result of hygiene or cleaning activities.)
- Ensure new risks are not introduced unintentionally, such as changes to processes or the installation of PV panels on combustible panels or EV charging points in close proximity to buildings.
Transfer
Most organisations already transfer risk through insurance and it may be a condition of financiers that full cover is in place. If an organisation is happy with the current premiums and levels of protection and terms, and if alternative provision could be easily obtained, it may only be necessary to consider limited further risk management. However, this is not the case for most businesses.
Managing the risk
Where composite panels are in place, the above measures require active management to reduce the risks presented by combustible core material. Typically, other key measures required by insurers, include:
- Identify panels and document the insulation materials, associated hazards and location within the facility. Where construction information is not present, core sampling may be required. Please note if panels were installed prior to 1995/6, they will not be LPS1181/ FM4880 approved, although may well be non- combustible panels (such as rockwool). This is a valuable exercise, as insurers typically assume the worst and have various requirements around the percentage of combustible construction. They may also consider the location of combustible panels in relation to higher risk inception areas, such as hot cooking areas and forklift truck charging facilities.
- Panels should be completely sealed with a metal facing and joints, and be maintained in good condition. A weekly documented inspection plan should be undertaken and, where damage has exposed the core insulation material, then metal caps or covers should be riveted to the panel. (Silicone is not suitable as it shrinks under heat, potentially exposing the core in the event of a fire).
- Power tools and cutting equipment should not be used on composite panels. A strict regime of ‘hot work controls’ should be implemented on any works undertaken within buildings that contain composite panels.
- Arson is a significant risk. No external combustible storage should be within 10 metres* of the main fabric of the building, and perimeter security integrity and CCTV coverage should also form part of the arson risk assessment.
- Electrical and other services that penetrate panels should be fitted with non-combustible, fire rated sleeves to the full thickness of the panels. Equipment and cabling should be subjected to frequent electrical testing and thermographic inspections.
*stack height also needs to be considered
Risk Engineering support from PIB
PIB Risk Engineering has a wealth of experience helping clients manage the challenges presented by composite panels in the food industry, and each of our fully trained, in-house risk engineers has over 20 years’ risk management experience within the insurance industry.
Unlike many of our competitors, we offer core risk engineering support as part of our overall service proposition. With an in-depth understanding of the operational challenges you face, we can help you plan to mitigate risks in an appropriate, cost effective and operationally possible manner, ensuring you retain control of the improvement programme and timescales, while we work in partnership with your insurers.
Our risk insight approach enables us to identify and communicate accurately the level of risk and current controls in place, creating certainty for the underwriters of the risk they are considering and significantly improving the response from the market.
Practical support includes:
- Help in identifying and communicating the risks to the insurance market through our risk insight survey approach
- Assistance in reviewing remedial measures, challenges to implementation and obtaining cost effective risk transfer from the insurance market.
To find out how PIB can help your food and drink manufacturing organisation to manage the issues of combustible composite panels and associated risks, and achieve greater business resilience, please contact David today